Glass Art Sculpture
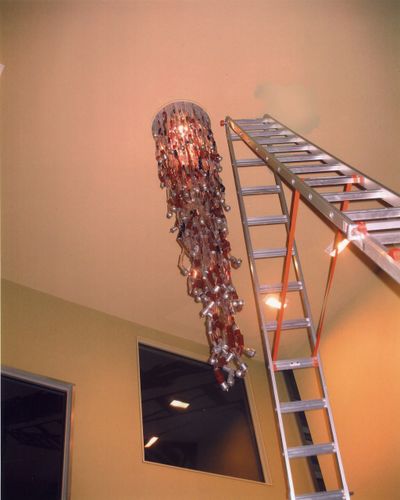
Transformation Through Art
Transformation Through Art
The physicality of working hot glass fits perfectly with my Mercurial personality and resilient attitude who’s worked as a licensed mental health therapist for over 25 years.
The experiences of life shape us, altering our perceptions and shaping the way we think and believe. I see the same alchemic parallel in creating glass sculptures using heat to sculpt and alter molten liquid glass into something of my imagination. My glass pieces represent the various adaptations and abstractions of self.
Trained and licensed as a mental health professional- sculpting glass has been a part of my therapy. I find clarity and peace in the material. It is my wish for you to experience emotion evoked by my work, and that you feel happiness.
My process of glass casting begins with ladeling glass from a furnace that holds about 600 lbs. of molten hot glass. We use recycled clear glass windshields and bottles at my studio. These broken up pieces are shoveled into the furnace, and melt over the course of 24 hours into a molten consistency that pours much like the thickness of honey. The only difference is that it is 2350 degrees Fahrenheit- much unlike honey!
I was born in New Orleans, LA and live between Nola (as its called), and Los Angeles, CA. I entered my Masters Program in Social Work at Tulane University in 1995 and took an elective studio class “Beginning Glass Art” taught by Gene Koss. It was love at first sight. The physicality of working hot glass fit perfectly with my love of physicality and fitness.
I have taught glass casting as an assistant in: Toyama-Japan; Pilchuck Glass School- Stanwood, WA; Penland School of Crafts-North Carolina; Urban Glass-Brooklyn, NY; First City Art-Pensacola, FL, and Tulane University in New Orleans, LA.
I have created one of a kind cast and blown glass pieces for Hilton Hotel, restaurants, galleries, and I am in private collections worldwide including His Holiness the Dalai Lama.
I see human nature in the material of glass. The heat and trials of life shape us, changing our internal edges and borders, just as heat shapes glass. My glass pieces are formed in the same manner. I approach creating my work from this mindset.
Giving Back is a value of mine, so In 2010
I created and founded “The Yes Foundation, INC” a 501(c)(3) to teach persons with disabilities using wheelchairs to blow and cast glass.
In 2016 I received a US Patent for my invention of a modified workbench that participants in wheelchairs can cast and blow glass from safely.
The CHAIR-iot facilitates ADA compliance in the glass art world.
The CHAIR-iot is in use at the Bergstrom Mahler Museum of Glass in Neenah, WI.
Learn more and purchase a CHAIR-iot for your studio or industry at: https://www.theyesfoundationinc.com
Me shaping glass in the "Cold Shop" on a belt sander